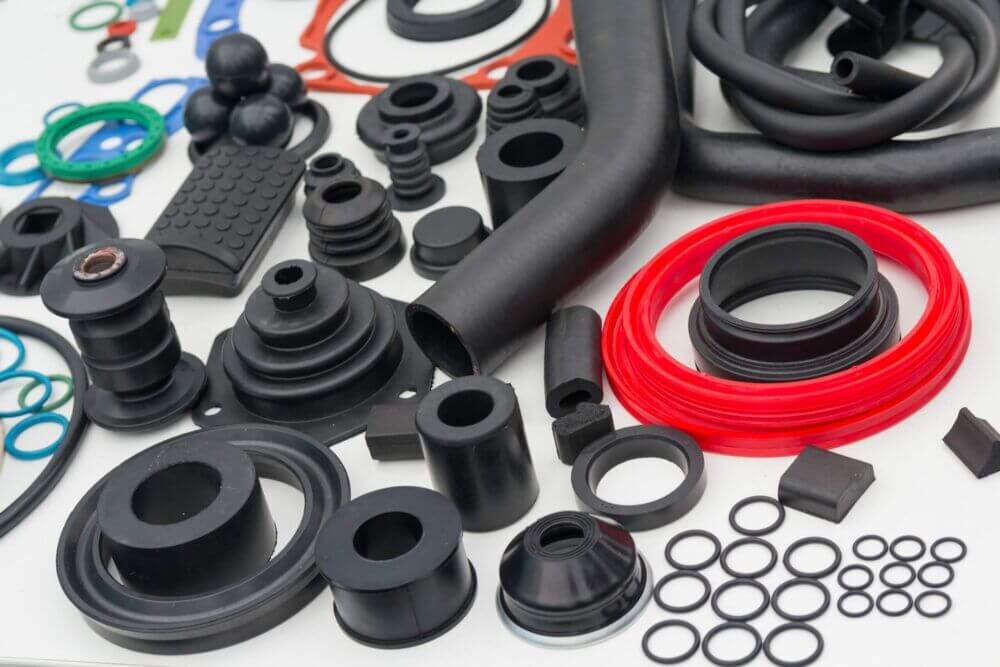
Introduction
Polymeric materials play a crucial role in various industries, and two prominent categories, thermoset and thermoplastic materials, exhibit distinct characteristics and applications.
The primary distinction between Thermoset and thermoplastic materials lies in their molecular structures and thermal responses. Thermosets undergo irreversible cross-linking during the initial forming process, resulting in a rigid three-dimensional network. Once set, they cannot be remolded or reheated without undergoing degradation. In contrast, thermoplastics have a linear or branched structure, allowing for reversible phase transitions when heated. This enables them to be reheated, remolded, and cooled without significant chemical changes. Thermoplastics generally have lower melting points, facilitating malleability at lower temperatures, while the cross-linked structure of thermosets provides higher temperature resistance, allowing them to maintain structural integrity under elevated temperatures.
This comprehensive comparison aims to explore the attributes, advantages, disadvantages, and applications of both, aiding in the selection of the right material for specific use cases.