A Reputation Built on Manufacturing Excellence with Quality Guarantees @GEMS-MFG
GEMS quality engineers incorporate quality into your product from the design phase to mass manufacturing process, which is planned ahead of time to lessen lead times, reduce risks, and improve the end product’s quality.
In keeping with our quality concept of “Right First Time,” we strive to deliver zero faults to our customers. Not only does this require scientific quality planning and modern manufacturing analysis, but it also demands a commitment to our employees’ technical growth. Our quality department is manned by a specialized team of quality specialists who are trained to validate and control all injection molding, die casting, machining, assembly, and finishing operations to ensure that they meet the drawing specifications and surpass the customer’s expectations.
GEMS-MFG has put quality control systems in place to assure complete customer satisfaction. We understand that your product reflects your company and brand, and that you cannot afford to cut corners. Being one of our customers, you will benefit from our customized, flexible production build and functionality test services. To ensure that your products maintain high performance levels, we combine efficient procedures with comprehensive quality control system. We are proud of ourselves on meeting and exceeding customer expectations on a regular basis.
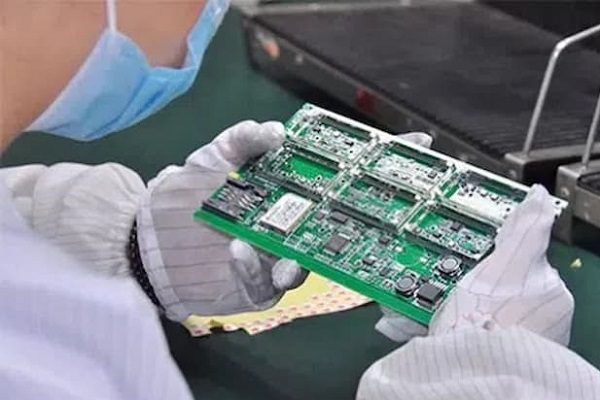
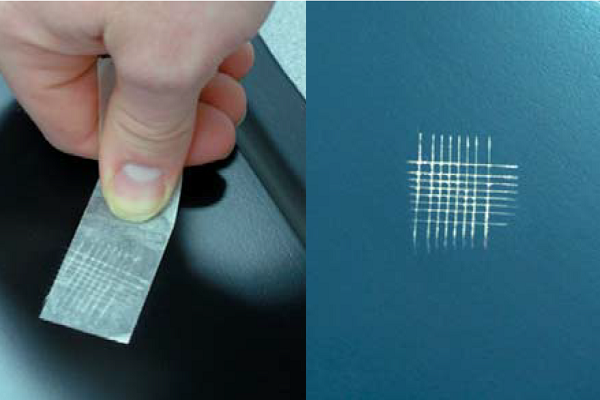
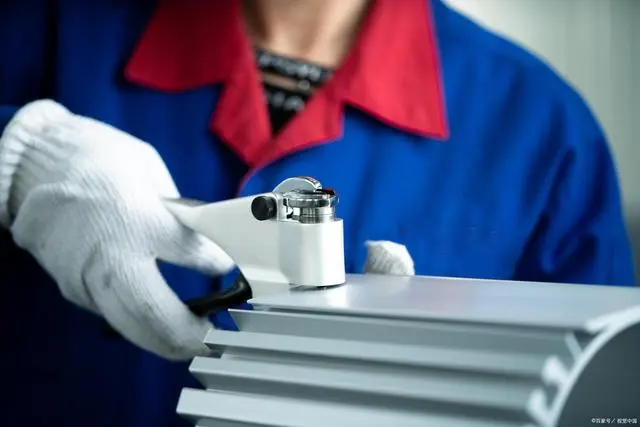
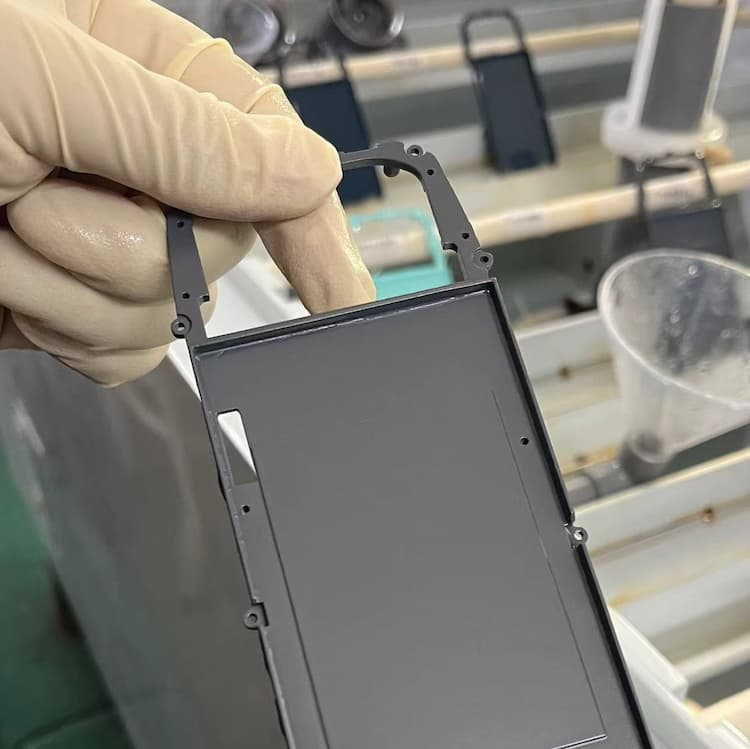
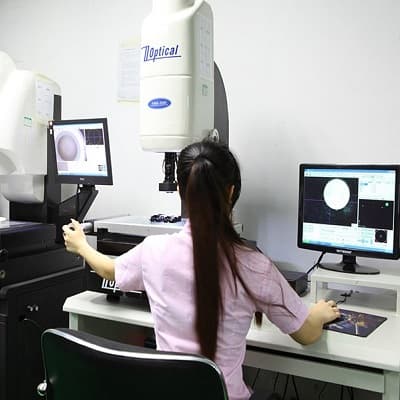
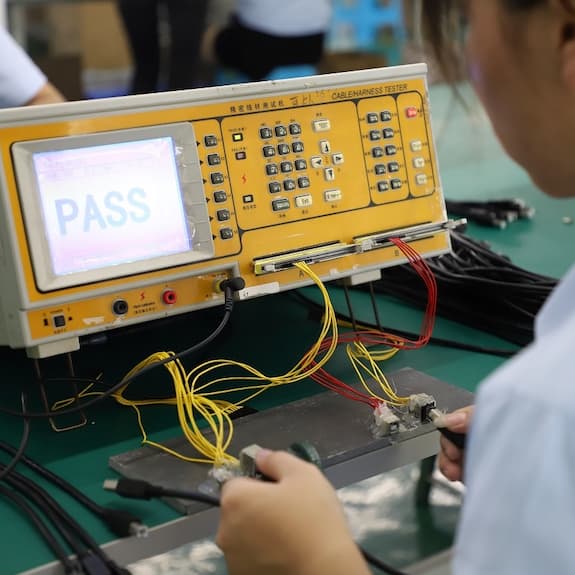
1. Quality Objective
Our first priority is customer satisfaction that is obtained through superior quality, customer service and continuous improvement.
2. Quality Management System
Quality Assurance is one of the most important elements of forming long-term and mutually beneficial manufacturing partnerships. GEMS Manufacturing has a system in place to make sure that we all components and assemblies manufactured for our customers is produced in a cost effective and timely manner while meeting their engineering specification and quality standard.
- Our Quality Management System will define the requirements for meeting our business needs, complying with regulatory requirements and the tools to be used for establishing, reviewing and measuring our quality objectives.
- We are all directly responsible for our Quality Management System’s dedication and compliance, as well as verifying its suitability and continuously enhancing its efficacy in order to improve our customers’ satifaction.
- All of our workers are charged with building quality in rather than inspecting flaws out, as driven by our customers’ needs and expectations. The production facilities and procedures are set to meet the product specification under industry certifications, regulatory registrations and compliancy levels, .
3. Quality Control Stages
At GEMS Manufacturing, we employ a three-stage QA/QC process to ensure quality and consistency with every part we produce.
- PRE-PRODUCTION – process, supplier, and material audits to ensure that all specifications and certifications are met or exceeded.
- PRODUCTION – We verify every part after each stage of the fabrication process, from programming to finishing.
- POST-PRODUCTION — Quality control techniques that are ISO certified and carried out by highly educated engineers. Additional diemensional and cosmetic checks are undertaken right before packing.
4. Quality Assurance Equipments
GEMS has excellent metrology capabilities in addition to our extensive manufacturing capabilities, including CMM, VMS, comparator, digital and mechanical measuring instruments, and a variety of attribute gauging to perform all required dimensional inspection and testing, ensuring that all customer specifications are reached. This focus allows us to routinely rank among our clients’ top-rated quality suppliers.
To fulfill your whole product lifecycle requirements, we offer complete product reliability testing, inspection, and qualification capabilities. We can focus on designated areas or testing criteria to validate client concerns or reaffirm the reliability of specific functionality, and our quality and product assurance team conducts product life testing and thorough circuit characterization to guarantee that designs meet or exceed necessary requirements. We can test to a variety of industry standards, and we’ll work with you to design custom test procedures that will allow you to analyze certification risks early in the product development lifecycle, lowering costs and speeding up time to market.
Quality Management Practices @GEMS-MFG
1.Leverage our knowledge to reduce risk
We take the time to understand your individual requirements and how the product is applied in the field, whether you need to assemble a few plastic pieces with metals, integrate a printed circuit board (PCB) into an enclosure, or create a more complex assembly product. We use disciplined component traceability data to analyze variables and make advantage of our experience to decrease risk, ensuring a robust and reliable product.
2. Solving problems before they arise
Throughout the product lifecycle, our quality process ensures great results. We utilize a full set of tools, including computational and experimental analysis to eliminate costly faults, reworks, re-qualifications and overhead demands that drain resources. We also go over each design to make sure it’s free of flaws that could create production issues or lower the quality of your final product. By addressing and resolving issues early, we optimize manufacturing after the product reaches the production floor, utilizing multifunctional cooperation and proactively lowering risk.
3. Higher Standard, Greater Confidence
We have the competence and knowledge to work with a wide range of businesses that require metal, plastic, and silicone parts to be manufactured following product design or customer concept ideas. Our quality control department is dedicated to ensuring that every component and finished product dispatched from our facilities is in great operating order and meets our high quality standards as well as the functionality expectations demanded by our clients.
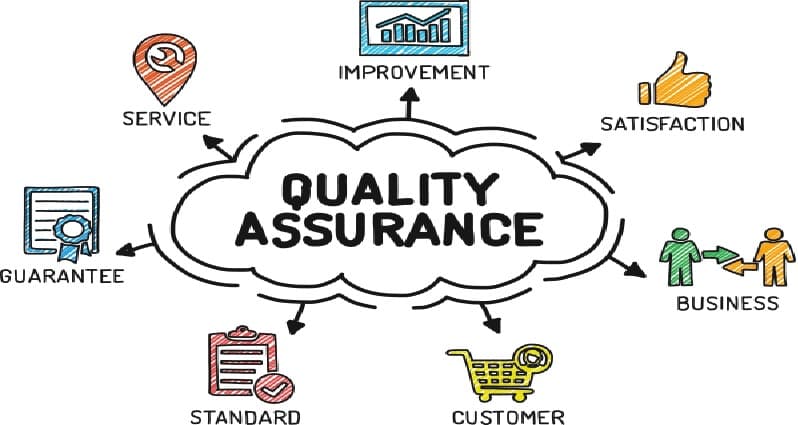