Die Casting Mold Making
GEMS is a global contract manufacturer of die cast molds to generate precision Magnesium products, Aluminum parts and Zinc components. When our engineers are involved early in the project, they can help design a tool and part specifically for mass production in consistent quality manner. All of our customers receive insight and expertise throughout all stages of the project. Our tool and die making services include thorough and diligent inspections using high caliber instruments and devices to ensure a quality controlled level of processing accuracy. We will submit engineering samples for evaluation & testing and provide quality reports as necessary till the approval of mass production. Throughout the life of the tooling, we carry out ongoing inspection and maintenance, and we keep complete tool history documentation. Our engineers offer die casting mold making solutions for a variety of industries including consumer electronics, automotive, healthcare, and more. For more information about our company or our tool and die design services, contact us directly.

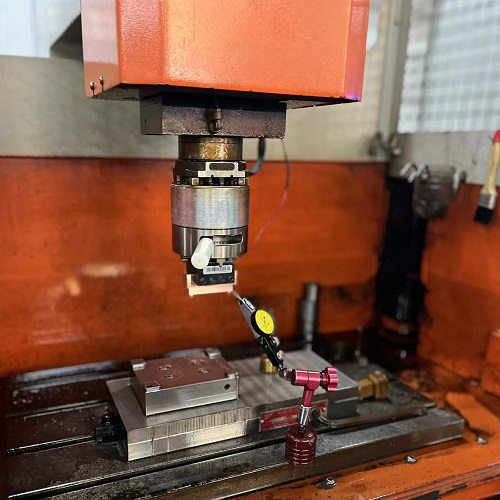
A quality die casting begins far before the die is ever built. Tooling design is one of our strengths. Working with customer specifications, we consider all aspects of the product design and how the metal will flow within the tool to build dies that produce geometrically complex parts to near net shape. We can help your organization to finalize a casting part design that meets your requirements and expectations while optimizing manufacturability to keep costs and defects to a minimum. We build molds from high-quality tool steel implementing strategies such as predictive wear analysis, and these molds are well checked and maintained before/ after every production run. This means fewer disruptions to your organization and longer life on your tooling investment.
Types of Die Casting Dies – Die Casting Molds Types
- Single cavity die– straight forward, has only one cavity
- Multiple cavities die– has more than one cavity but they are all identical
- Family die– also has more than one cavity but they are of different shapes
- Unit die – completely separate dies (also called exchangeable inserts) can be assembled into a master holding die to make varied components
Types of metal materials we use for Die Casting:
- Magnesium Alloy
- Aluminum Alloy
- Zinc Alloy
They are normally non-ferrous and their mechanical properties vary greatly to fit almost every type of application a manufacturer may need.
The Common Properties of Die Casting Alloys:
- Good corrosion resistance
- High strength and hardness
- High thermal conductivity
- High electrical conductivity
- Outstanding EMI/RFI shielding properties
- Good finishing characteristics
Magnesium Die Casting / Aluminum Die Casting / Zinc Die Casting
For the die casting process, your metal material is melted and then transferring into a steel mold- also known as a tool or a die. These die casting molds or die casting tool or casting steel dies allow us to form the metal into the shape of each component with accuracy and repeatability that you need for your project . Once the mold is filled it has a brief cooling off period to allow the metal to harden. With our history of innovation to die casing manufacturing processes, we design and build tools for richly-featured parts with variable wall thickness, holes, threads, internal features, and other necessary elements to avoid secondary operations.