Liquid Silicone Rubber (LSR) Injection Molding Supplier in China
LSR molding differs slightly from thermoplastic injection molding due to its property. While the traditional reaction of Plastics Injection Molding process focuses on a pressurized impingement mixing process, Liquid Injection Molding is comprised of a mechanical mixing method that blends a two-component compound together in a mold. Since LSR is a thermosetting polymer, its molded state is permanent—once it is set, it can’t be melted again like a thermoplastic.
Liquid silicone rubber (LSR) is a family of materials commonly specified for gaskets, seals and cushioning pads in portable communications, data acquisition devices, sensing instruments and rugged enclosures with demanding sealing requirements in outdoor conditions. Liquid Silicone Rubber materials include standard silicones and specific grades to fit various part applications and industries like medical, automotive, infant care, general industrial markets, aerospace, electronics, and many other specialized industries.
As one of the global integrated injection molding companies, GEMS Manufacturing works proudly with liquid silicone rubber (LSR) injection molding. Actually, injection molding of liquid silicone rubber (LSR) has been becoming one of the fastest growing segments of GEMS operation. We have the manufacturing expertise to provide services that range from prototyping to serial production of high-precision components. We use steel molds that offer large quantity affordable tooling and accelerate manufacturing cycles, and stock certain amount of various grades and shore of LSR materials for quick turnaround service. Our liquid silicone rubber molding facilities can produce custom production parts and end-use products in 30 days or less. When the production run is complete, parts or assembly products will be properly packed and shipped shortly to fulfill customer demand. Up to date we have produced millions of liquid silicone rubber parts for customers worldwide.
Here are the primary steps involved in the liquid silicone rubber injection molding process:
- The uncured liquid silicone starts in two containers, Compound A and Compound B, which connects to the pumping system. Barrel A holds the base-forming material, and Barrel B contains a catalyst. A metering unit automatically releases the two substances at a constant one-to-one ratio, as well as any pigmentation additive.
- The molder can program and customize the automated injection-molding machine and have the injection setting deliver the appropriate shot size for each job. The platens and pistons, which align and close the mold, have settings for the temperature, pressure, injection rate, and cycle time-adjusted in accordance with the customer’s specifications
- After the completion of the setup, the molding machine heats the mold to the appropriate temperature and applies the appropriate clamping force. The mold closes in coordination with the machine’s injector, pump, and supply. The injection mechanism then pushes the material into the mold and cavities.
- A combination of heat and pressure applied to the liquid silicone rubber cures the material until it solidifies. Upon completion of the cycle, the mold opens, and the part and flashing can be removed automatically or by a worker. Then, the mold closes and repeats the process.
- After the removal of the item from the mold, the post-molding process may include de-flashing, post-curing, inspection, and packaging.
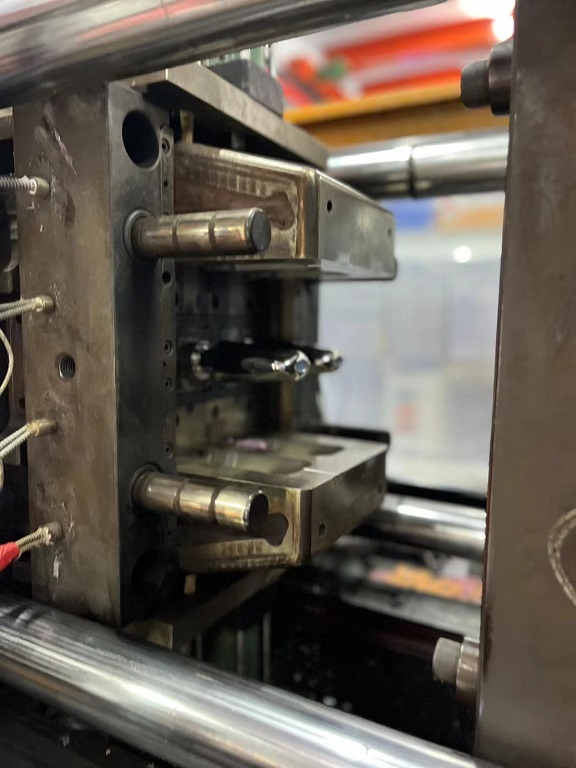
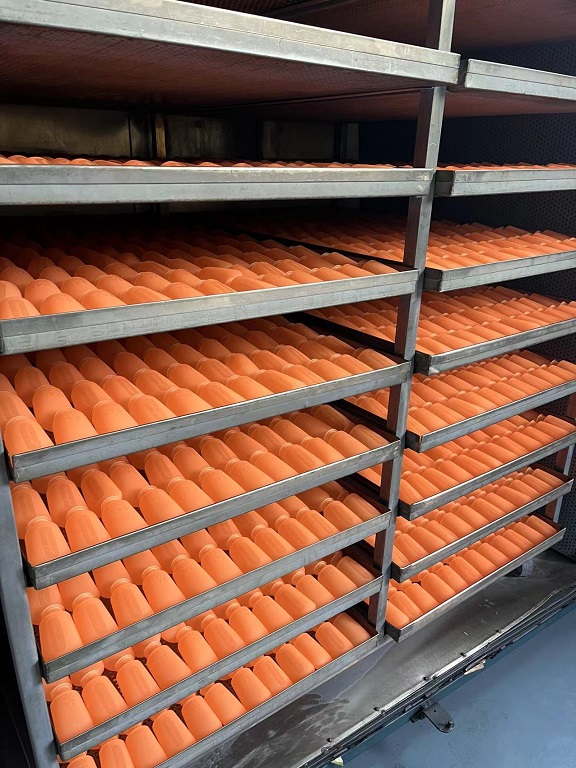
The endless possibilities of liquid silicone rubber
The growing popularity of LSR products can be explained by its range of exceptional properties. These result from the chemical structure of the compounds, which is based on a set of strong siloxane bonds that are more stable and offer superior strength compared to carbon bonds. The properties of LSR span the spectrum of needs, making it a versatile compound for numerous uses.
- First, LSR compounds are exceptionally durable and resistant to extreme temperatures and environments. These materials offer functionality at temperatures as low as -60°C and as high as 250°C. LSR compounds do not stretch even at high temperatures and they retain their flexibility in the cold.
- Besides, LSR compounds are strong, flexible and stable, offering superior performance over long periods of time. They can be electrical and thermal insulators, enabling excellent conductivity preservation.
- Furthermore, the compounds are highly inert, biocompatible and hypoallergenic, which means they can be used for components that are in close contact with the human body, such as prostheses or artificial organs. These compounds can degrade, however, when in contact with base or highly acidic environments – this should be taken into consideration.
- Finally, including but not limit to, LSR compounds can be produced in any imaginable colour due to the transparent nature of the material, which is then pigmented to blend into any required shade. LSR can even be coloured to match the wide spectrum of human skin tones.
And from a production perspective, LSR items can be made in high volumes with fast cycle times, automated processes, and little waste. LSR molded components are tasteless and odourless. These parts are used in a wide variety of settings. Further key properties of this versatile material include: Flame retardant, Intense weatherability, Steam- and humidity-resistant, Absorbs vibration, Resistant to corrosion, Mould and mildew resistant , UV stable.
So, it is easy to see why LSR products have become so popular in so many industries. LSR compounds are useful in the medical, cosmetics and food industries because they are non-reactive and non-toxic. In the automotive industry, their heat-resistance makes them ideal for use close to engines. They are useful in any application that involves electricity. LSR compounds are also ideal for the manufacture of products comprising of complex parts that must be manufactured at high speeds, without any loss of precision and considering the upmost productivity.
To sum up, LSR is a material that can be used for an immeasurable number of applications – on condition that you consult with industry experts about its suitability and production. It is also important to be aware that LSR is not for everyone and all applications, despite its myriad uses and benefits. An expert can tell you when LSR is the best compound for your project, GEMS can help take your manufacturing into reality with stable output.