GEMS Manufacturing: Your Trusted Partner for HCR Molding Service in China
When seeking HCR molding services, industry players turn to GEMS Manufacturing, a distinguished provider based in China. With a proven track record and a commitment to excellence, GEMS-MFG offers comprehensive solutions in the realm of High Consistency Silicone Rubber molding.
1. Expertise in HCR Material Formulation:
GEMS Manufacturing distinguishes itself through its expertise in formulating and processing HCR materials. The company’s research and development efforts contribute to the creation of custom HCR formulations that meet the exacting standards of clients across various industries.
2. Cutting-Edge Technology and Advanced Processes:
Equipped with cutting-edge technology, GEMS Manufacturing employs advanced molding processes to ensure precision and consistency in every component produced. The integration of automation and rigorous quality control measures sets GEMS-MFG apart as a leader in the field.
3. Quality Assurance Throughout the Process:
GEMS Manufacturing places a strong emphasis on quality assurance throughout the HCR molding process. Rigorous testing protocols and comprehensive inspection procedures are implemented to guarantee that each component meets the highest quality standards.
4. Tailored Solutions for Diverse Industries:
Whether it’s seals and gaskets, automotive components, or medical devices, GEMS-MFG provides tailored solutions to meet the unique requirements of diverse industries. The company’s versatility and commitment to innovation make it a preferred choice for clients seeking reliable HCR molding services.
5. Global Reputation for Excellence:
GEMS Manufacturing’s ability to provide fast, high-quality service at a low cost has led to a global reputation for commitment to customer satisfaction. The company’s team of injection molding experts for HCR & LSR can assist clients through the entire process, from material formulation to the production of precision components.
In conclusion, High Consistency Silicone Rubber (HCR) molding stands as a versatile and reliable method for producing silicone rubber components with specific performance attributes. GEMS Manufacturing, with its dedication to excellence, technological prowess, and material expertise, plays a pivotal role in delivering high-quality HCR molding services. As technology continues to advance, HCR molding remains at the forefront of silicone rubber manufacturing, offering a cost-effective solution for industries demanding precision, durability, and versatility in their components. GEMS Manufacturing stands ready to be your trusted partner in navigating the complexities of HCR molding for your unique applications.
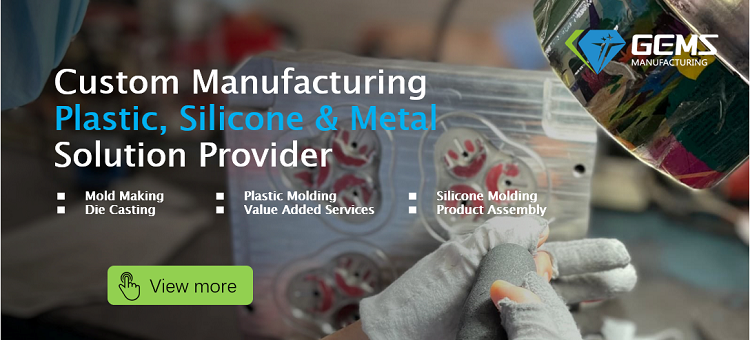