VI. Conclusion
In the dynamic landscape of medical device manufacturing, the choice between Liquid Silicone Rubber (LSR) and High Consistency Rubber (HCR) molding processes holds profound implications for product quality, performance, and regulatory compliance. This comprehensive overview has illuminated the distinct characteristics, advantages, and applications of LSR and HCR in the context of medical device production.
Through case studies, it’s evident that the choice between LSR and HCR is contingent upon project-specific requirements, design intricacies, and production limitations. LSR distinguishes itself with its precision and biocompatibility, whereas HCR may offer advantages in terms of durability and mechanical properties. Moreover, the integration of LSR over hard plastic substrates exemplifies the innovative potential of LSR technology in combination product development, opening avenues for novel manufacturing approaches and enhanced product functionalities.
Moreover, the expertise of silicone manufacturers, such as GEMS-MFG, plays a pivotal role in guiding medical device OEMs through material selection, process optimization, and regulatory compliance. Collaboration between OEMs and silicone manufacturers facilitates the seamless integration of silicone elastomers into cutting-edge medical devices, ensuring adherence to stringent standards and optimal performance in clinical settings.
In essence, the comparative analysis between LSR and HCR underscores the critical importance of selecting the right material and molding process to meet the evolving demands of the medical device industry. Whether striving for precision, durability, or innovation, the strategic utilization of LSR and HCR technologies paves the way for transformative advancements in medical device manufacturing, ultimately enhancing patient care and shaping the future of healthcare.
If you’d like additional information on Liquid Silicone Rubber (LSR) Molding & High Consitency Rubber (HCR) Molding, as well as their flexible integrated applications, please feel free to contact us GEMS-MFG!
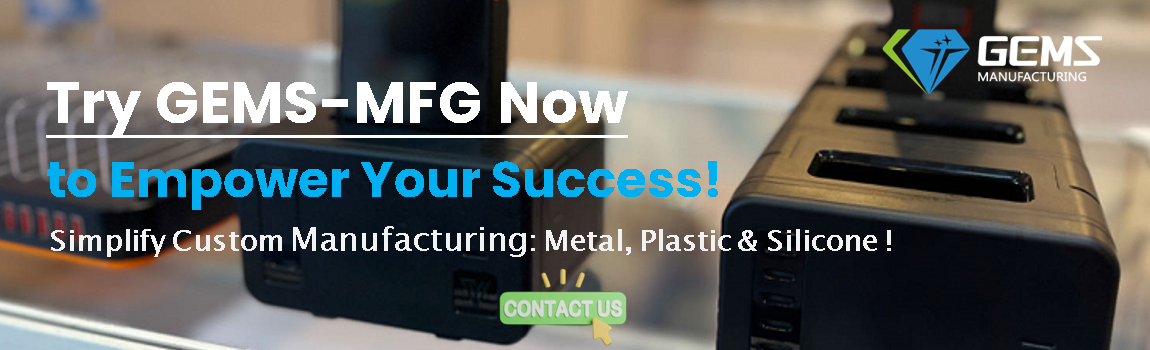