VI. Conclusion
In conclusion, MIL-A-8625 stands as a cornerstone in the realm of anodizing specifications, delineating precise requirements for the treatment of aluminum and its alloys in military and aerospace applications. Through its classification of various anodic coating types and classes, this specification ensures that anodized components exhibit exceptional corrosion resistance, wear resistance, and durability, meeting the stringent demands of critical industries. From chromic acid anodizing to hard anodize processes, each type offers unique properties tailored to specific application needs, while the distinction between Class 1 and Class 2 coatings further refines performance expectations. As anodized aluminum finds widespread utility in aerospace, military, automotive, electronics, and architectural sectors, adherence to MIL-A-8625 guarantees the consistent delivery of high-quality, reliable, and long-lasting products capable of withstanding the harshest environments and operational challenges.
Are you looking for a reliable supplier to use DFM process for your projects? GEMS-MFG is the comprehensive solution provider here for you. As a one-stop custom manufacturer, we provide a wide range of services, including 3D printing, mold making, injection molding, CNC machining, die casting, and more. Whether your requirements involve intricate prototypes or precision parts, GEMS-MFG is committed to delivering an efficient and cost-effective solution tailored to your needs. Contact us today to explore our offerings and receive an instant quote. Your manufacturing goals are our priority @GEMS-MFG.
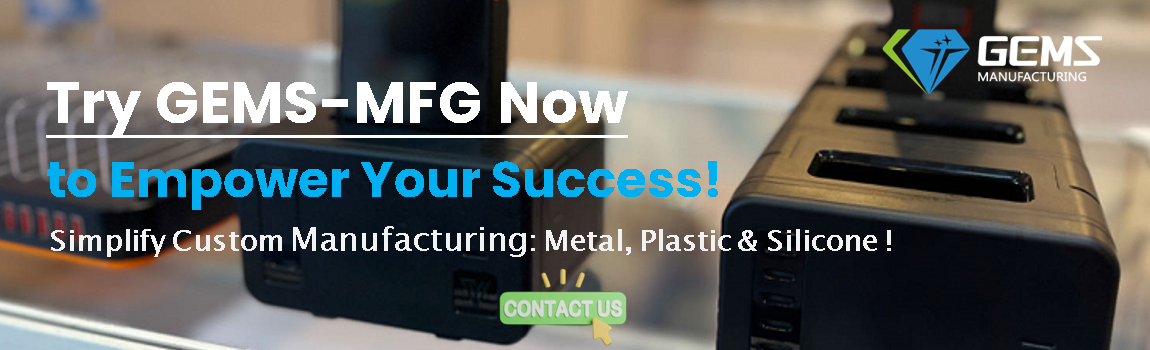