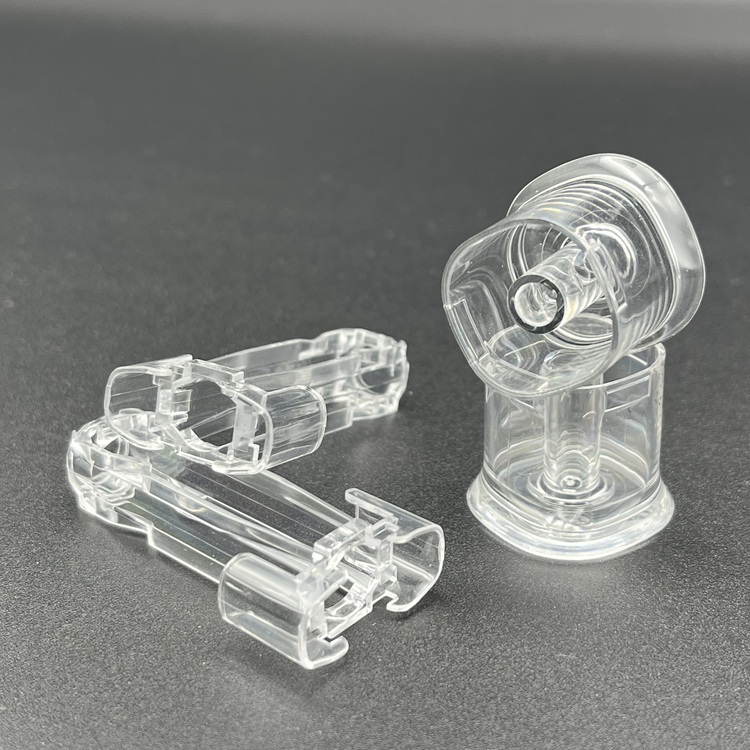
I. What is Tritan Copolyester?
Tritan copolyester is a new-generation copolyester that offers a unique balance of processing and performance properties — including clarity, toughness, and heat and chemical resistance, and the ability to produce products free of bisphenol-A (BPA). It is a class of polymers formed through copolymerization, where two or more monomers are polymerized together. Tritan is manufactured by Eastman Chemical Company and is known for several key characteristics:
1.1. Clarity:
Tritan copolyester offers excellent clarity, similar to that of glass, making it a popular choice for products where transparency is desired, such as water bottles and food containers. Approximately 90% light transmittance and good gloss. Tritan copolyester demonstrates a high level of light transmittance, a low level of haze and a consistent color. Resulting high gloss makes colors more vibrant in colored or tinted applications.
1.2. Durability:
It is highly durable and resistant to impacts, making it suitable for use in products that need to withstand everyday use and potential rough handling. Notched Izod results are comparable to PC. Tritan copolyester is impact- and shatter-resistant and has the ability to withstand extreme conditions. Excellent hydrolytic stability and chemical resistance; low residual stress. Tritan is not just dishwasher-safe, but will stay clear and tough even over hundreds of cycles with resistance to crazing or cracking.
1.3. Safety:
Tritan is often marketed as being free from bisphenol A (BPA) and other potentially harmful chemicals, making it a safer alternative for food and beverage containers. It offers a BPA-free option that provides as-molded toughness and chemical resistance without annealing.
1.4. Heat Resistance:
Tritan copolyester can withstand relatively high temperatures without warping or releasing harmful chemicals, making it suitable for use in dishwashers and microwaves.
1.5. Chemical Resistance:
It is resistant to a wide range of chemicals, including many household cleaners and common chemicals found in food and beverages, reducing the risk of degradation or contamination.
1.6. Ease of Processing:
Tritan copolyester can be easily molded and formed into various shapes, allowing for the production of complex designs and customized products.
These properties make Tritan copolyester a versatile material used in a variety of applications, including water bottles, baby bottles, food storage containers, kitchenware, and medical devices. Its combination of clarity, durability, safety, and chemical resistance has made it a popular choice for manufacturers looking to create high-quality and reliable products.