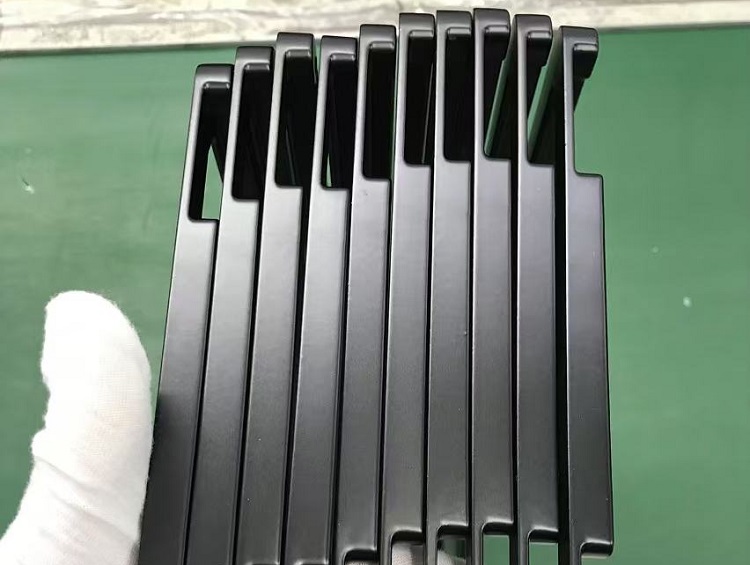
I. Introduction of Magnesium Die Casting
Magnesium die casting is a pivotal manufacturing process known for producing lightweight, high-strength components with intricate geometries. Widely used in industries such as automotive, aerospace, and consumer electronics, magnesium die-cast parts are celebrated for their versatility. However, the reactive nature of magnesium alloys demands specialized surface finishing techniques to ensure durability, aesthetic appeal, and functional reliability. This guide provides expert tips for achieving optimal surface finishes on magnesium die-cast parts.