IV. Conclusion
The 2K injection molding process, using specialized two-shot molds or two-component molds, has revolutionized manufacturing by enabling the efficient production of complex, multi-material components in a single molding cycle. By combining two different materials—whether for functional, aesthetic, or performance-enhancing purposes—2K injection molding significantly reduces the need for post-production assembly while improving part precision and durability. The integration of 2K molds into various industries, from automotive to medical devices and consumer electronics, highlights the versatility and efficiency of this process. However, it also comes with challenges such as ensuring material compatibility, mold complexity, and troubleshooting potential defects.
When executed with the right materials, precision mold design, and proper quality control, 2K molding proves to be a powerful tool in modern manufacturing. Its ability to streamline production while enhancing product functionality makes it a valuable technique for companies looking to stay competitive and innovative. As the demand for multi-functional, aesthetically appealing, and durable products grows, the significance of 2K injection molding will only continue to rise, solidifying its place as a cornerstone technology in the manufacturing industry.
Are you looking for a reliable supplier to use 2K Mold in injection molding process for your projects? GEMS-MFG is the comprehensive solution provider here for you. As a one-stop custom manufacturer, we provide a wide range of services, including 3D printing, mold making, injection molding, CNC machining, die casting, and more. Whether your requirements involve intricate prototypes or precision parts, GEMS-MFG is committed to delivering an efficient and cost-effective solution tailored to your needs. Contact us today [INFO@GEMS-MFG.COM] to explore our offerings and receive an instant quote. Your manufacturing goals are our priority.
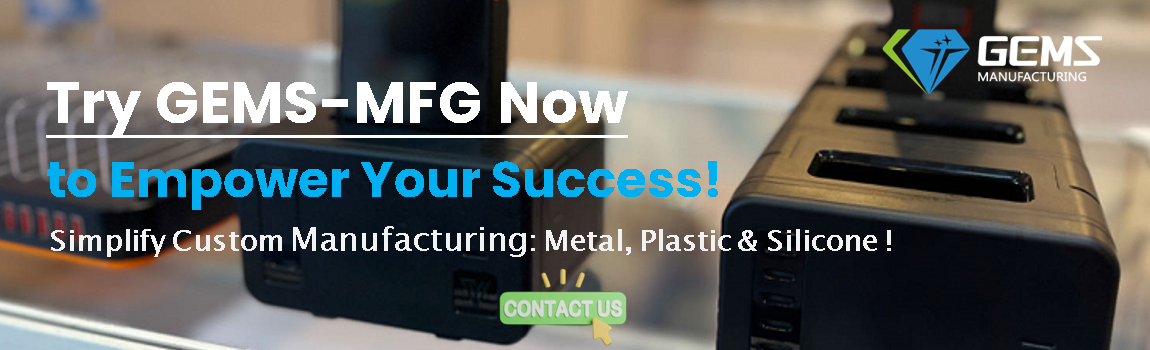