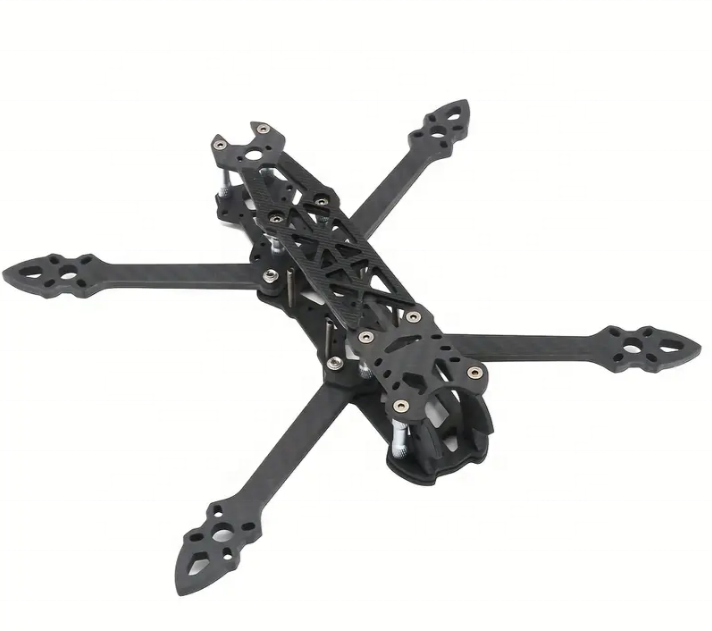
I. Introduction
In today’s rapidly evolving technological landscape, the demand for advanced materials that offer superior performance, lightweight properties, and enhanced functionality has never been greater. Among the myriad of materials available, carbon fiber and aluminum-magnesium alloy emerge as standout contenders, each boasting unique characteristics and promising applications across various industries.
In this comprehensive comparative analysis, we are going to delve into the world of carbon fiber and aluminum-magnesium alloy, exploring their material properties, manufacturing processes, advantages, limitations, and application areas. By comparing these two materials side by side, we aim to provide engineers, designers, and manufacturers with valuable insights to inform their material selection decisions and drive innovation in product development.
Join us as we embark on a journey to uncover the unparalleled capabilities of carbon fiber and aluminum-magnesium alloy, paving the way for groundbreaking advancements and transformative innovations in engineering and manufacturing.