Consult with A Manufacturing Expert for Your Logo Printing
Your logo represents your business and brand. As a result, it must be memorable, eye-catching, and, above all, unique. A corporation can raise brand awareness and differentiate itself from competition by branding a product with an exclusive logo. That’s what we can best support from the production side to supply products with customized logo and branding solutions to meet your unique needs.
When deciding among screen printing, pad printing, and laser etching, it’s not really a case of which process is the best in general but which approach is most fit for your particular printing project. It’s wise to study your product application and think about the results you want to achieve before choosing which printing method to execute the production. Rest assured that when you work with GEMS Manufacturing, you’ll get expert advice on the best imprint process for your finished product with neat logo and branding, which instantly help your brand stand out and leave imprints in the customers’ minds.
Key Methods Available for Custom Logo And Branding @GEMS-MFG
At GEMS Manufacturing, we have a good knowledge of applying different logo imprinting technologies to create your custom logo in one or two colors, or even multi-colors. Over our years of practice, silk-screen print, pad printing and laser etching are proved to be top 3 processes that are commonly used.
1. Screen Printing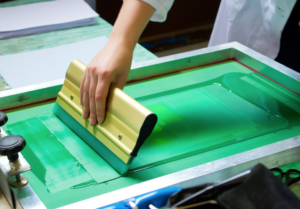
Screen printing, also known as silk screening, is a technique that may be applied on a variety of products with different shapes, sizes, and substrates. A stencil is applied to a screen (or a series of screens). The ink is applied on the screen, and a roller or squeegee is used to push the ink through the stencil and onto the substrate below. On a product, we can reproduce a tiny or huge image. Screen printing is a fantastic option for single or multiple colors printing in both short and long runs, and it has been used to print artwork on textiles and other materials for centuries. Screen printing equipment has evolved to the stage that it is highly complex and largely automated in certain applications. It’s the best for printing large images quickly and efficiently, rather than the ones with intricate details. Screen printing is widely used by organizations and companies all around the world for brand awareness, promotional products, and marketing. Screen printing is also used to print warnings, information, and directions for utilizing mechanical or electrical instruments on printed semi-conductor, electronic, control panel, machinery and many others.
2. Pad Printing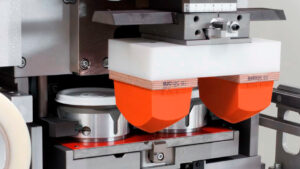
Pad printing’s name reveals a lot about how it works. Pad printing is a relatively new technology as compared to screen printing, which has been used for centuries and is typically chosen since it provides possibility and convenience for the printing of unusual shaped products. The process involves transferring ink from a silicone pad to the object to be printed. You could compare it to the stamps you probably used as a kid to make crafts — though professional pad printing is clearly far more advanced and complicated! The pad printing machine stabilizes both the pad and the product before pressing it into an ink plate that has been customized to the shape of your brand or artwork. After that, the pad is pressed onto the object and left to air dry, a rather simple process. Pad printing has a number of advantages, including the ability to print on three-dimensional surfaces and items of all shapes and sizes. This printing method will still produce a high-quality print even if your objects are curved or have an uneven surface. Pad printing is also appropriate for products that are delicate or mechanically sensitive. If you need to print fine subjects, you’ll realize that pad printing has a far better resolution than screen printing.
3. Laser Etching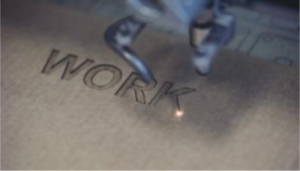
“Laser marking,” “laser printing,” and even “laser pad printing” are all terms used to describe laser etching. Laser marking is full digital, but what does this means? To begin with, this means that no work tools such as screens or tools are required. The design is given to the machine in a CAD format via software, which is far more flexible, especially when revisions or customization are desired in the design. Neither chemical materials such as inks, paints, and solvents, nor curing and drying stages, are required for laser etching process. As a result, the entire marking process is accelerated. For some applications Laser etching or laser marking a device is a more durable alternative than pad printing. The disadvantage of laser marking is that parts can only be marked in grey and the material must be loaded with a laser-reactive additive, but the benefits often outweigh the drawbacks.
4. Injection Molded Marking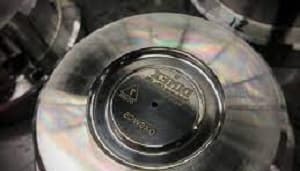
In Injection Molding, logos can be integrated directly into the mold, allowing the branding to be a fundamental part of the product design. This ensures long-lasting branding, especially for high-volume production. Besides, when building a injection part with such molded logo, it eliminates the time and expesne of secondary process, which is the most cost effective solution from manufacturing perspective.
Custom Capabilities for Logo Branding @GEMS-MFG
At GEMS, we offer comprehensive logo and branding solutions that integrate seamlessly into our manufacturing processes, ensuring that your brand’s identity is showcased on every custom part. Our capabilities span various materials, including Metal, Plastic, and Silicone Parts, covering processes like Rapid Prototyping, Injection Molding, CNC Machining, Die Casting, and Finished Product Assembly.
1. Colour Matching
We can formulate a wide range of worldwide standard colors, including Pantone, RAL, and HKS. We can also create custom proprietary colors based on your design concept or requirements.
2. Artwork Vectorizing
Customers frequently do not have the original artwork on file and instead have low-resolution pixel graphics, such as jpg, bmp, and tiff. If you are experiencing this issue, please email us your file; for a small cost, we may have it redrawn and vectorized. This solution is offered to help our customers save money on labor and time-consuming processes.
3. Printing Fixturing
We can manufacture the appropriate fixtures for logo imprinting or layer etching. Fixturing can be tailored in nylon, aluminum, urethane compounds, and a number of other materials based on the customer’s application and technical drawings.
4. Test Printing
Our engineering test lab enables us to perform trial prints on your products, and if necessary, we can even help you deliver your prototype samples for actual touching and evaluation, so that you can avoid problems early in the design process and avoid costly fixes later.
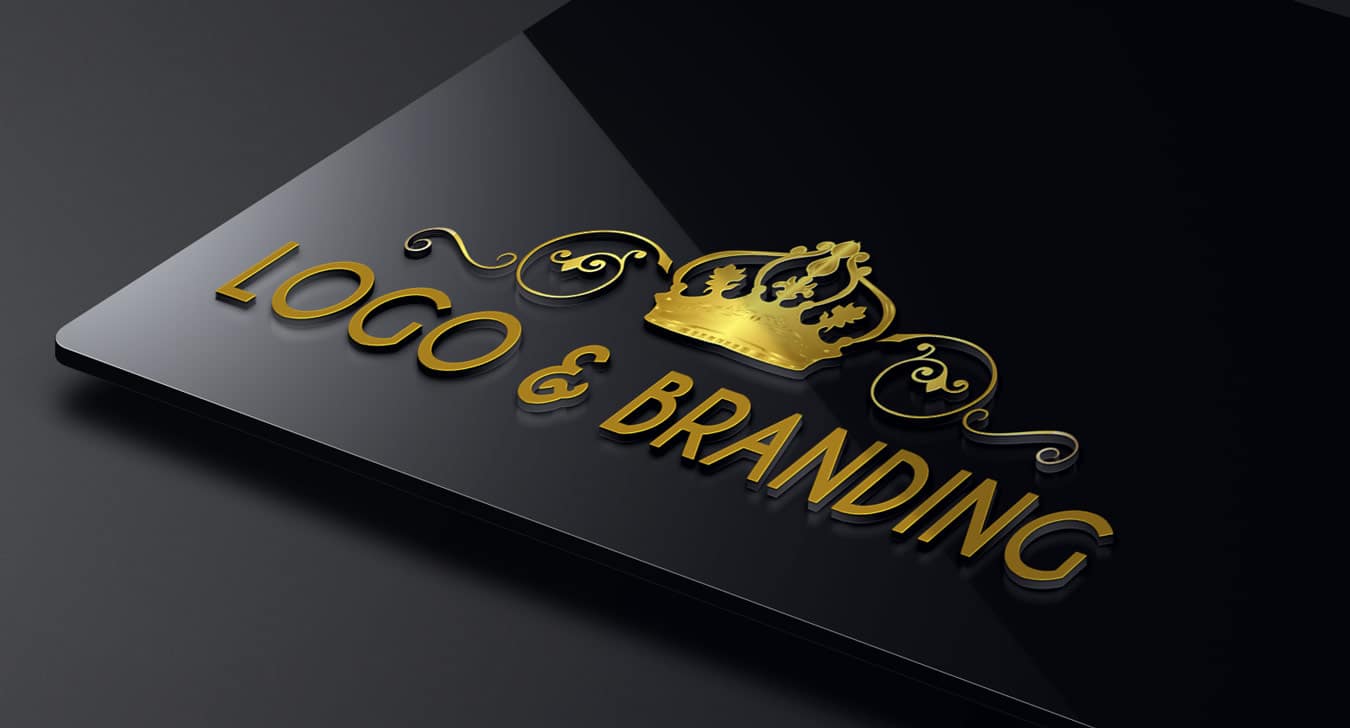