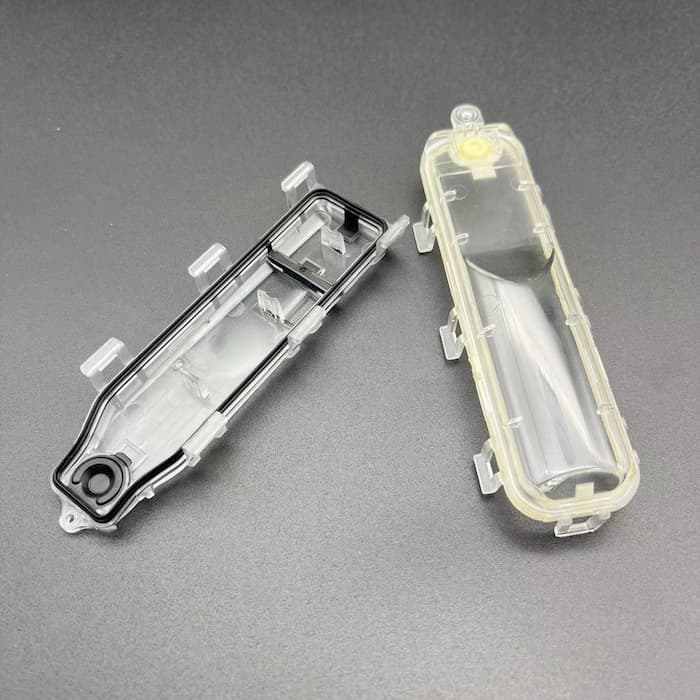
I. Introduction to TPE Material
Thermoplastic Elastomers (TPE) represent a versatile class of materials that combine the elasticity of rubber with the processability of thermoplastics. Unlike traditional thermoset elastomers, which undergo irreversible curing processes, TPEs can be repeatedly melted, molded, and recycled, making them environmentally friendly and economically viable. This unique combination of elastomeric and thermoplastic properties allows TPEs to exhibit characteristics such as flexibility, resilience, durability, and ease of processing.
TPEs are composed of a polymer matrix and a filler material, typically rubber or thermoplastic, which imparts the desired properties to the material. Depending on the specific composition and processing techniques, TPEs can range from soft and flexible materials with a Shore A hardness of 0 to 100, to harder and more rigid materials with a Shore D hardness of up to 70 or higher. This wide range of hardness options makes TPEs suitable for a diverse array of applications across various industries.
TPE materials can be processed using conventional thermoplastic processing techniques, such as injection molding, extrusion, and blow molding, making them highly versatile and adaptable to different manufacturing processes. This versatility, combined with their excellent mechanical properties, chemical resistance, and weatherability, has led to the widespread adoption of TPEs in industries such as automotive, consumer goods, electronics, medical devices, and more.
Obviously, TPEs offer a unique combination of elastomeric and thermoplastic properties, making them an ideal choice for applications that require flexibility, resilience, and ease of processing. Their recyclability, chemical resistance, and processability further enhance their appeal, making TPEs a preferred material solution for a wide range of manufacturing applications.