Plastic Injection Molding Service In China
Injection molding is a popular manufacturing process for producing large quantities of plastic parts from materials called thermoplastics. It’s the process of melting plastic, injecting it into a mold then repeating the process to make thousands or even millions of the same part.
Whether making 1 part or 1,000,000 parts, GEMS Manufacturing have set up Scientific Production Molding Program, a proven system of checks and balances to make sure your parts are produced correctly and on time. GEMS Manufacturing uses thermoplastic materials; both engineering and commodity grades. There are numerous grades and options for plastic material choices, plus new, innovative products are readily available. An example of the products processed and manufactured here are ABS, PC/ABS, Nylon, Acrylic, Acetal, polyester, polystyrene, polyethylene, polypropylene, PPO, PPS plus thermoplastic rubbers.
In addition to these grades, purpose-driven materials are offered including food grade, medical grade with UL yellow card listings and automotive grades. These products are available with additives for strength and other disciplines. Some additives we process include glass (both short & long fiber), carbon, conductive, non-conductive, anti-static, anti-microbial, fire retardant, lubricative, wear resistant, talc, calcium, UV stabilizers and more. Colors available are any color in the rainbow.
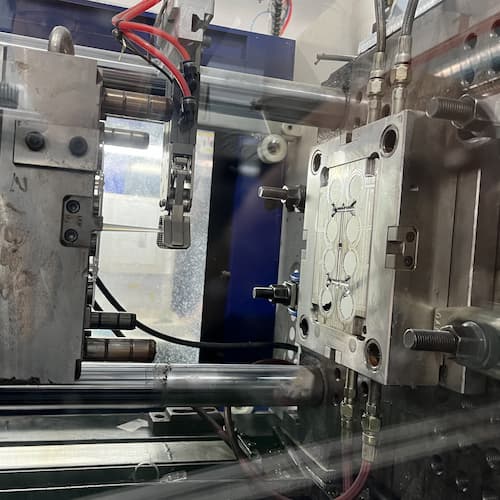
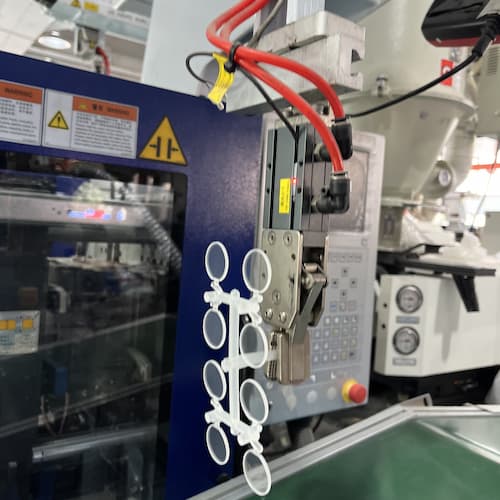
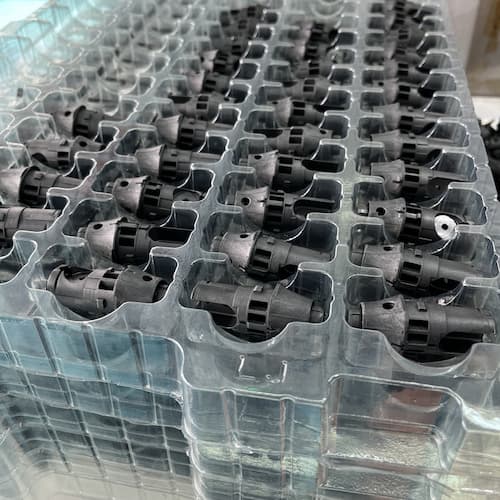
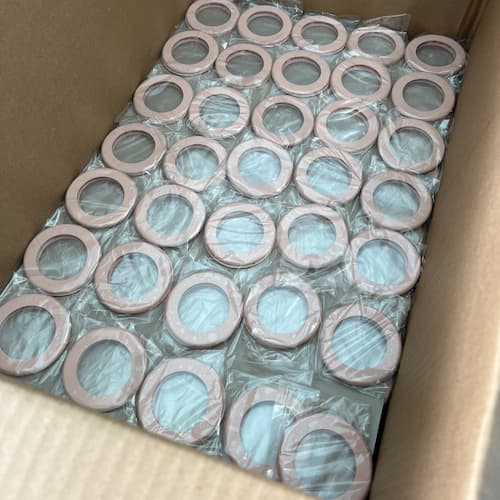
Common Defects in Plastic Injection Molded Parts
While each molded part is unique and there is no universal remedy for all molding defects, there are common quality-related issues which can be resolved with simple adjustments to either the machine conditions or the mold design. Consulting is included and recommended. Many unknowns will happen when not cultured in the plastic injection industry.
The table below highlights 5 common defects and their probable causes, which can assist you in determining and correcting the issue to ensure a quality molded part. Other problems that can occur include; parts not to print, warp, non-uniform part shrinking, deformations, trapped gas, flow lines, weakness, jetting, discoloration, brittleness, delamination, gate blush, weld lines, voids and more.
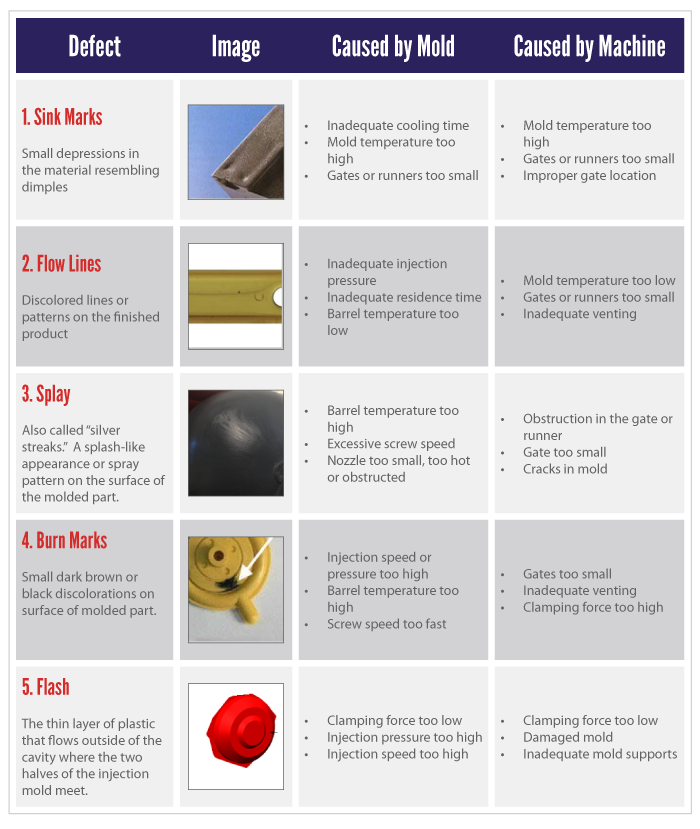
While above defects are the most common causes for components being scrapped in the injection molding process, they aren’t the only problems that can happen. Working with an experienced injection molding supplier who has the capability to spot potential defects and the knowing-how to prevent them is one of the greatest supply chain management strategies to avoid injection molding troubles. With strong backup by in-house mold making and regular mold maintenance services, GEMS takes pride in its experience and expertise in injection molding manufacturing, which allows us to offer high-quality products free from defects.