Your Magnesium Die Casting Partner @GEMS-MFG
In summary, surface finish in magnesium die casting is a multifaceted aspect that encompasses surface quality, treatment techniques, and advanced analysis methods. It plays a pivotal role in the functionality, durability, and aesthetics of magnesium components, making it an indispensable element of the manufacturing process. Achieving the desired surface properties requires a meticulous approach, from mold design and casting to post-processing and quality control.
Therefore, in the world of magnesium die casting, your business partner like GEMS-MFG can be the key to unlocking your company’s full potential. We can bring expertise, custom solutions, quality assurance, cost efficiency, and timely delivery to the table. With a collaborative and sustainable approach, we help you succeed in today’s competitive manufacturing landscape, ensuring a long-lasting partnership built on trust and excellence. Choose your business partner for magnesium die casting wisely, and watch your manufacturing endeavors reach new heights of success. To get started, please request a quote through our convenient online form or call us.
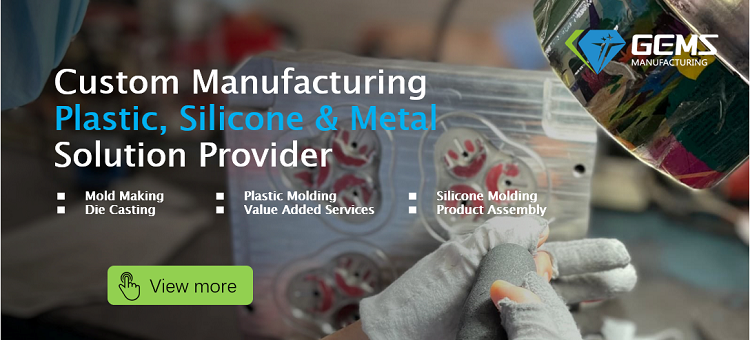