Your custom SPI mold Partner @GEMS-MFG
Merely looking at an injection mold classification chart is not sufficient, since each mold classification has its own distinct parameters. Therefore, it is more important to collaborate with a molder who is well-versed in these mold standards and classifications. The guidance of the molder is crucial in choosing the most suitable mold type that aligns with your production requirements, cost considerations, and quality goals.
At GEMS-MFG, we specialize in manufacturing high quality plastic molds with custom SPI standard that always meet our customer expectations. We are very willing to share clients about our solid experience and expertise in mold making, so as to maximize productivity, reduce waste, and continuously improve production efficiency and safety. We look forward to helping you bring your custom SPI molds into fact. To get started, please request a quote through our convenient online form or call us.
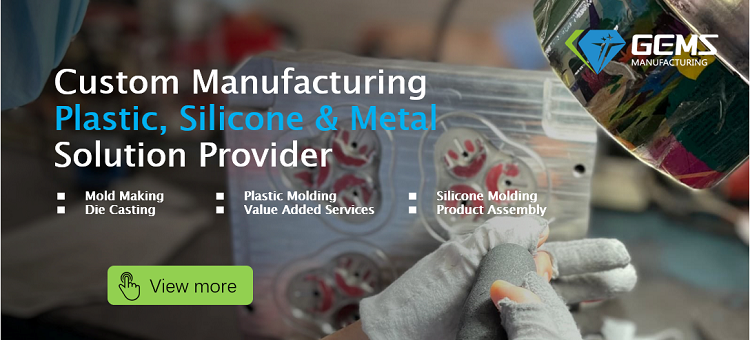