X. Conclusion
This comprehensive guide serves as an essential resource for injection molding factories, exploring the diverse properties, applications, and future developments of Acetal and Delrin (Polyoxymethylene or POM). The journey begins with an in-depth look at their general properties, highlighting exceptional machinability and mechanical characteristics, making them ideal for precision-molded components.
Delving into the distinction between Delrin and Acetal, the guide clarifies their terms, offering valuable insights into material selection based on project requirements and budget considerations. The exploration extends to their chemical resistance, flammability, and challenges in adhesion, providing crucial considerations for optimal usage. Real-world applications and case studies showcase the versatility of Acetal and Delrin across industries, from automotive components to medical devices and consumer electronics. The guide concludes by looking ahead to future developments, anticipating advancements in material formulations, manufacturing processes, and environmental impact mitigation.
In essence, this holistic guide empowers injection molding professionals to make informed decisions, ensuring the optimal use of Acetal and Delrin for precision, durability, and sustainability in diverse applications. If you have any specific questions or if there’s anything else you’d like to know, feel free to ask us GEMS-MFG!
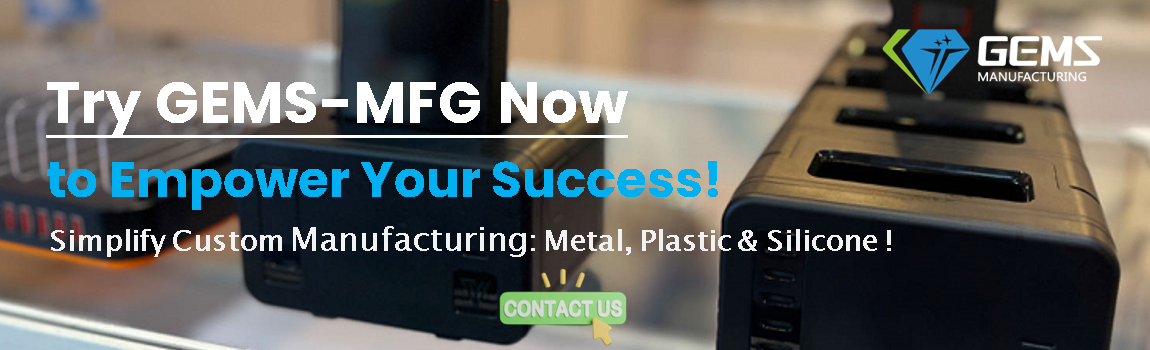