Silicone Rubber Mold Making
Liquid Silicone Rubber (LSR) and High Consistency Rubber (HCR) are two families of silicone rubber. Liquid silicones are generally made from two part systems that are mixed and heat cured. LSRs can be casted into sheets or injection molded. HCRs are often mixed and supplied to manufacturers in gum form to be compression molded or rotocured into sheets.
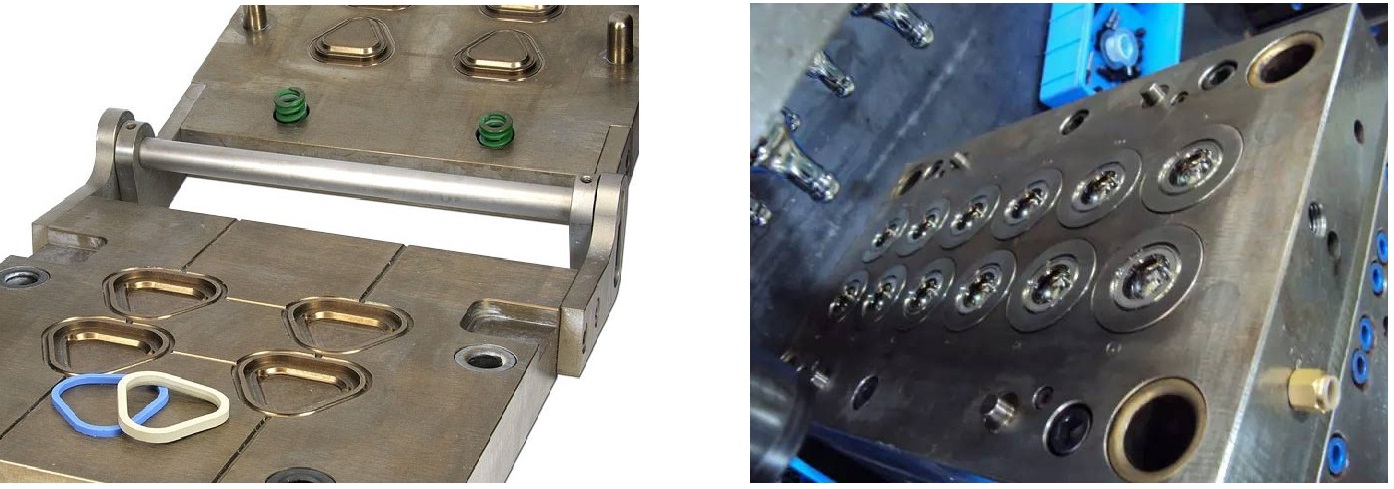
Solid Silicone Rubber (HCR)
- Processing is highly variable
- Better mechanicals / tougher
- Wider temperature range
- Lower sheet cost
- Faster production time
- Better compression set resistance
- High flexibility for small-to-medium series
Liquid Silicone Rubber (LSR)
- Two part system
- Short cycle times (low viscosity, high curing speed)
- Process can be fully automated
- Molds with up to 256 cavities
- Suitable for complex part geometry
- 2K injection molding
- No secondary finishing
How to define LSR or HCR Mold as the right option?
- Geometry of the part
- Properties specification
- Chemical / physical properties required
- Production run size
- Cost budget
- Liquid or solid silicone rubber
- What molding equipment is available
The Critical Adantages of Silicone Mold
Like a standard injection mold, an LSR molding tool is fabricated using CNC machining to create a high-temperature tool built to withstand the LSR molding process. Silicone is a strong choice for mold-making because it offers such a diverse array of benefits. You can easily create custom designs using silicone molding. The molds themselves are also quite durable, so you can use them repeatedly without fear of breakage. Silicone’s inorganic makeup—compared to rubber, its organic counterpart—makes it highly resilient to heat and cold, chemical exposure, and even fungus. Some of the benefits of silicone molds include the following:
- Flexibility
Silicone’s flexibility makes it easy to work with. Silicone molds are pliable and lightweight compared to stiffer substances like plastic and they’re also easier to remove once a part is fully formed. Thanks to silicone’s high level of flexibility, both the mold and the fabricated part are less likely to break or chip. You can use custom silicone molds to shape everything from complex engineering components to holiday-themed ice cubes or confections.
- Stability
Silicone withstands temperatures from -65° to 400° degrees Celsius. Additionally, it can have an elongation of 700%, depending on the formulation. Highly stable under a broad range of conditions, you can put silicone molds in the oven, freeze them, and stretch them during removal.
- Durability
In most cases, you’ll get many runs out of a silicone mold. However, it’s important to note that the life span of molds can vary greatly. The more frequently you cast, and the more complex or detailed your design, the faster your mold might degrade. To maximize the life of your silicone molds, clean them with mild soap and water, dry them thoroughly, and store them flat without stacking.