VIII. Conclusion
Magnesium alloy die casting delivers unmatched advantages for lightweight, high-performance components. By addressing design challenges and limitations, manufacturers can unlock its full potential for applications in automotive, aerospace, consumer electronics, and beyond. With continued advancements in surface treatments and die technologies, magnesium alloys remain a cornerstone for sustainable and innovative manufacturing.
Are you looking for a reliable supplier who is professional in Magnesium Die Casting that result in high quality assurance for your projects? GEMS-MFG is the comprehensive solution provider here for you. As a one-stop custom manufacturer, we provide a wide range of services, including rapid prototyping, mold making, injection molding, CNC machining, die casting, and more. Whether your requirements involve intricate prototypes or precision parts, GEMS-MFG is committed to delivering an efficient and cost-effective solution tailored to your needs. Contact us today [INFO@GEMS-MFG] to explore our offerings and receive an instant quote. Your manufacturing goals are our priority.
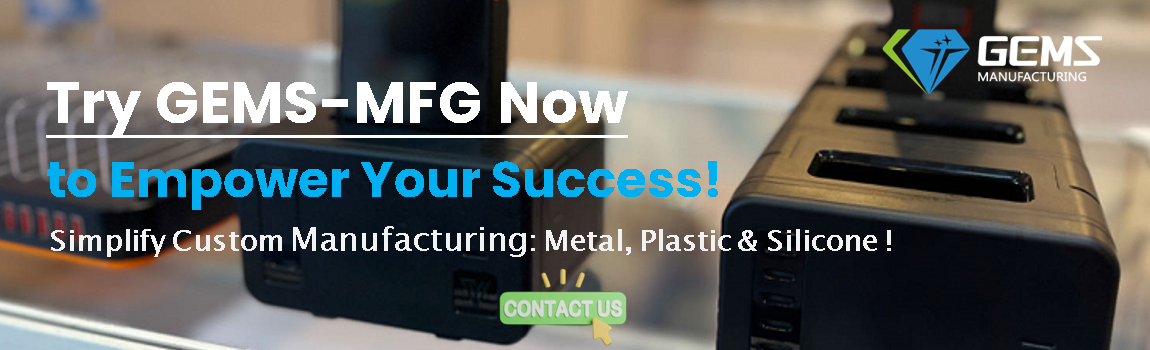