X. Conclusion
Lightweight metals, including aluminum, magnesium, and titanium, have emerged as critical materials in the modern manufacturing landscape. These metals are increasingly sought after for their excellent strength-to-weight ratios, durability, and versatility, making them ideal for a variety of industries, such as aerospace, automotive, medical devices, and consumer electronics. Throughout this article, we’ve explored their unique properties, manufacturing processes, and real-world applications, highlighting the pivotal role these materials play in driving innovation and performance.
Aluminum is often chosen for its machinability, cost-effectiveness, and lightweight characteristics, making it indispensable in sectors ranging from automotive to electronics. Magnesium, with its lower density, offers even lighter weight, making it a preferred choice for applications that demand reduced weight without compromising strength, such as in automotive components and drone manufacturing. Titanium, renowned for its exceptional strength, biocompatibility, and corrosion resistance, plays a critical role in high-performance and medical applications, where both durability and safety are paramount.
Manufacturing processes, such as CNC machining, die casting, and injection molding, have been integral in unlocking the full potential of these lightweight metals. CNC machining ensures high precision and tight tolerances, crucial for custom parts in aerospace and automotive industries. Die casting, especially with magnesium and aluminum alloys, allows for complex, high-strength parts that can be produced quickly and cost-effectively. Injection molding, using materials like aluminum alloys, facilitates mass production of lightweight parts with high consistency, essential for sectors like consumer electronics.
However, manufacturing lightweight metals comes with its own set of challenges. The complex nature of working with these materials requires careful consideration of factors such as material selection, heat treatment, and process optimization to ensure the final product meets the desired performance standards. Despite these challenges, the opportunities for innovation are vast, with lightweight metals continuing to drive advancements in manufacturing technologies and product designs.
As industries demand lighter, stronger, and more efficient solutions, the adoption of lightweight metals will only continue to grow. With ongoing advancements in manufacturing processes, these metals will play a central role in shaping the future of product design and manufacturing, from enhancing performance to contributing to more sustainable and energy-efficient solutions.
In conclusion, lightweight metals are not just a trend but a cornerstone of modern manufacturing. Their ability to combine strength, lightness, and versatility makes them invaluable in meeting the complex demands of today’s industries. By understanding the properties, challenges, and opportunities associated with these materials, manufacturers can continue to push the boundaries of what is possible, creating innovative, high-performance products that meet the evolving needs of global markets.
Are you looking for a reliable supplier who has abundant experience and expertise in providing lightweight metals that can result in high quality assurance for your projects? GEMS-MFG is the comprehensive solution provider here for you. As a one-stop custom manufacturer, we provide a wide range of services, including rapid prototyping, mold making, injection molding, CNC machining, die casting, and more. Whether your requirements involve intricate prototypes or precision parts, GEMS-MFG is committed to delivering an efficient and cost-effective solution tailored to your needs. Contact us today [INFO@GEMS-MFG] to explore our offerings and receive an instant quote. Your manufacturing goals are our priority.
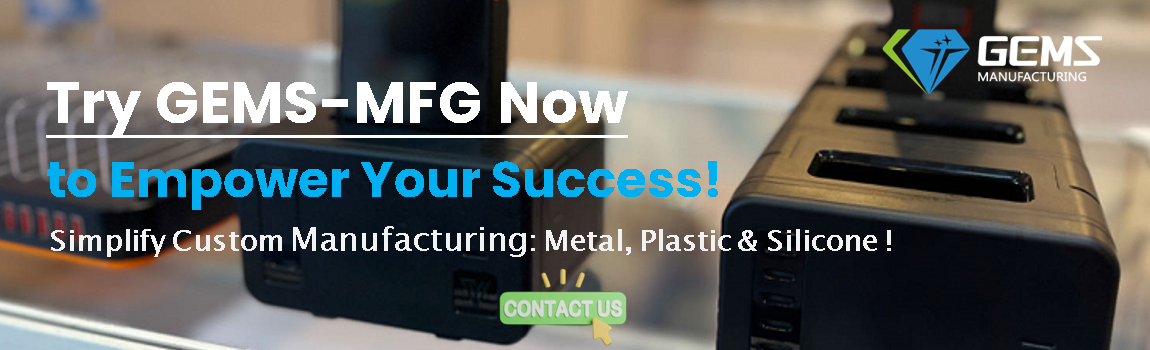