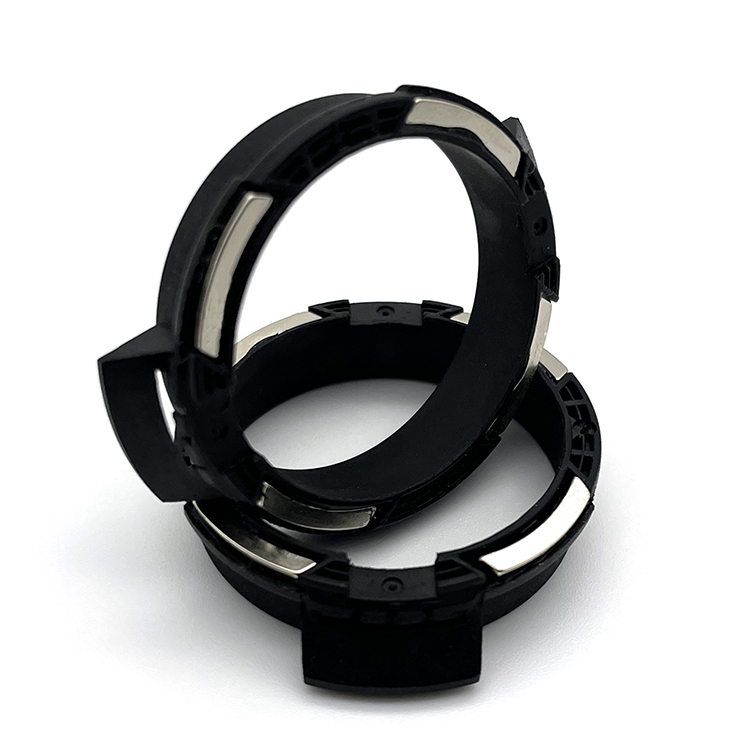
What Is Insert Molding?
In modern manufacturing, numerous products incorporate both metal and plastic components. Among the various production methods available to achieve this integration, insert molding stands out as the most widely used solution.
Insert molding is a specialized plastic injection molding process where a pre-formed component, often made of metal or another material, is inserted into the mold cavity before the plastic material is injected. The molten plastic then bonds to or around the inserted component, creating a single integrated part.