IX. Conclusion
“Crystal Clear Plastic Solutions: Injection Molding Transparent Plastic Products” explores the precision and expertise required to manufacture transparent and translucent plastic products using injection molding. The article highlights the process’s ability to deliver high-quality, visually flawless components tailored to various applications.
It begins by examining the unique properties of materials like Polycarbonate and Acrylic, emphasizing their role in achieving optical clarity and durability. Design optimization and process control are discussed as essential elements for ensuring consistent quality, with a focus on factors such as wall thickness, mold design, and temperature regulation. The challenges of working with transparent plastics, including surface defects and material sensitivities, are addressed alongside practical solutions that manufacturers use to overcome these issues. The article also provides insight into the diverse applications of transparent plastic products, from optical lenses and automotive lighting to medical devices and consumer electronics.By blending technical expertise with industry applications, this article demonstrates how injection molding enables manufacturers to produce innovative, lightweight, and aesthetically appealing solutions while maintaining exceptional clarity and performance.
Are you looking for a reliable supplier who has abundant experience and expertise in providing crystal clear plastic injection mold making and the injection molding that can result in high quality assurance for your projects? GEMS-MFG is the comprehensive solution provider here for you. As a one-stop custom manufacturer, we provide a wide range of services, including rapid prototyping, mold making, injection molding, CNC machining, die casting, and more. Whether your requirements involve intricate prototypes or precision parts, GEMS-MFG is committed to delivering an efficient and cost-effective solution tailored to your needs. Contact us today [INFO@GEMS-MFG] to explore our offerings and receive an instant quote. Your manufacturing goals are our priority.
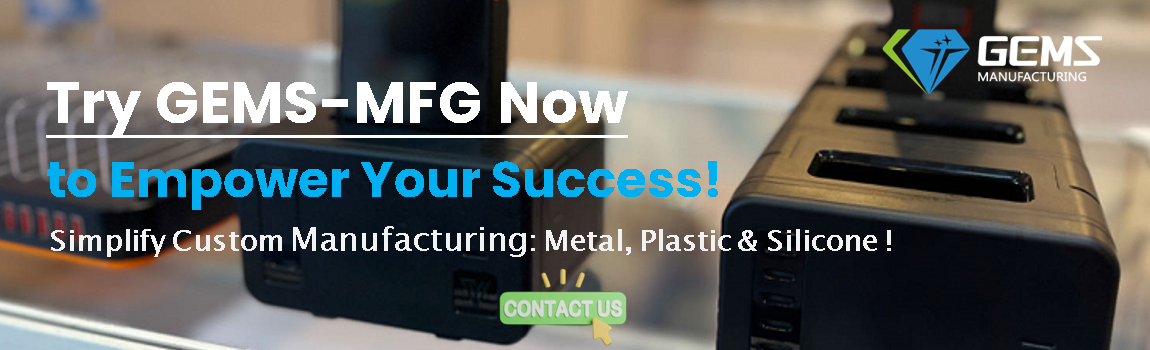