Case Brief:
As known to all, a good mold is the key to mass production of good quality parts. Even though running out of the tooling’s designed life, it is still not common to see crack lines on the core, cavity or slider blocks. So how shocked we were when one day an USA customer brought us a newly made die casting mold (medium size 600*550*650mm) with its core insert cracking in two separate halves. GEMS Manufacturing was the 4th factory to look into such nightmare case when the customer was totally desperate, as all the professionals told him a fully DEAD mold, however, they already signed a deadline contract to ship products by containers. What can we help?
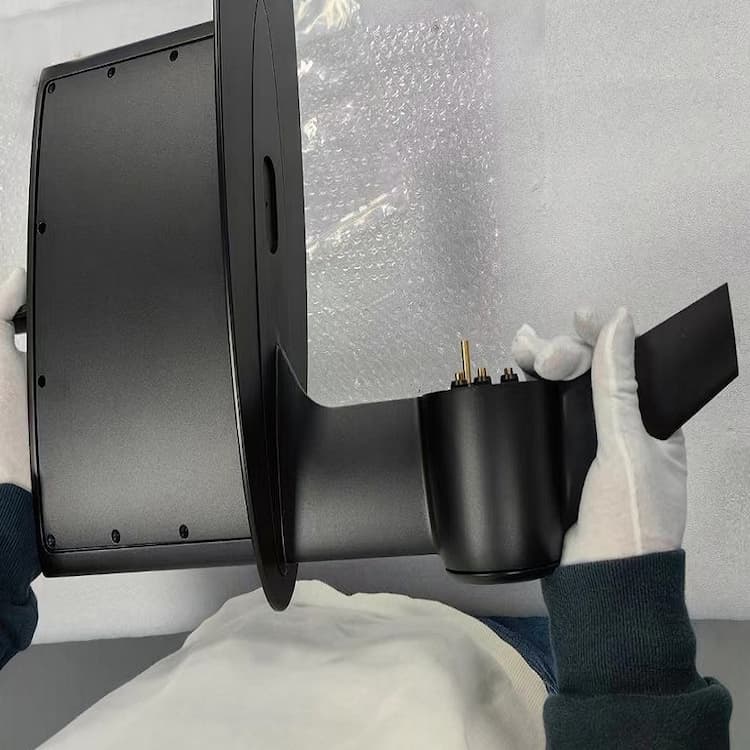
How the Story Goes:
The Problem
As known to all, a good mold is the key to mass production of good quality parts. Even though running out of the tooling’s designed life, it is still not common to see crack lines on the core, cavity or slider blocks. So how shocked we were when one day an USA customer brought us a newly made die casting mold (medium size 600*550*650mm) with its core insert cracking in two separate halves. GEMS Manufacturing was the 4th factory to look into such nightmare case when the customer was totally desperate, as all the professionals told him a fully DEAD mold, however, they already signed a deadline contract to ship products by containers. What can we help?
Our Solution
After a diagnostic assessment to the breaking mold, GEMS Manufacturing told the customer that maybe we could proceed a surgery to make it work for 5000 to 10000 shots with 10 days’ efforts. Of course, we frankly informed the client that it was not a guarantee; however, we were willing to involve in and try all means to save such a critical project.
The Result
And 7 days later the repaired tool was loaded on a die casting machine with constant output. I never forgot the night that the customer cried like a baby and hugged us everyone onsite so so tightly when the mold was proved to work. Without a doubt, it successfully finished the first production order for 7000 units. In fact, the tool still looked good when the second production mold (for replacement) built by GEMS was ready to take over the future die casting demand.