Let Surface Finishes Empower Your Innovation @GEMS-MFG
GEMS Manufacturing can help you proactively modify your product, component design or manufacturing process to increase quality and reliability, explain yield challenges and analyze the root cause of field failures by leveraging our industry-leading knowledge and expertise across multiple industries. With a diverse unit of talents and technology capabilities, our engineers are among the best in the business to address problems at any stage of the product lifecycle.
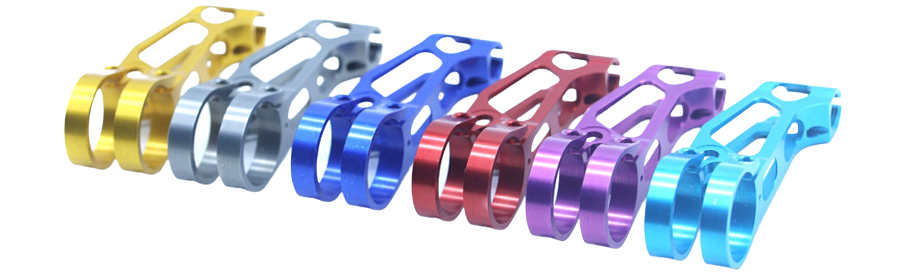
1. Optional Surface Finish Colors & Textures
Surface finish, sometimes known as surface texture or surface topography, is the nature of a surface as characterized by the three properties of lay, surface roughness and waviness. Specification of surface finish are typically found on technical drawings for mechanical parts, especially where parts have A surface, provide a soft touch, fit together securely, or work in extreme conditions. Each manufacturing process produces a surface texture, and it is quite typical to add an extra process (or multiple processes if required) to modify the initial texture in order to make the resulting texture more practical and affordable for long-term use of product lifecycle.
Upon your component has been designed you may be considering several sorts of surface finishes, and we want to supply you with a finished part that can be placed straightly into your assembly process, rather than a raw part to help you save money and streamline your operation. At GEMS Manufacturing, we offer the ultimate in value-added secondary operations for Surface Finish.
2. Common Surface Treatments
Texturing, Polishing, Anodizing, Bushing, Powder Coating, Oil Spraying, Sand Blasting, Heat Treating, Soft Touching, Chrome Plating, UV painting and so on. Find more details below, or contact us directly to discuss the best surface finish for your application.

- Polishing
If you need a smooth, non-textured finish, a buff polishing machine might be the way to go. This machine buffs the product’s surface with a cloth wheel, resulting in a high, glossy finish. The method is frequently used for decorative items that require gloss and smoothness. Buff polishing machines tend to smooth out a product’s edges, and the procedure is less successful for applications requiring delicate, fragile, or recessed features due to the cloth wheel’s range limitations. - Anodizing
Anodizing is an electrochemical technique that turns a metal surface into an anodic oxide finish that is decorative, long-lasting and corrosion-resistant. As known to all, aluminum is ideal for anodizing, other nonferrous metals like magnesium and titanium can be anodized as well. The anodic oxide structure is made completely of aluminum oxide and is derived from the aluminum substrate. This aluminum oxide isn’t applied to the surface like paint or plating; instead, it’s totally merged with the underlying aluminum substrate, so it won’t chip or peel. It has a porous, highly organized structure that allows secondary processes like coloring and sealing to take place. - Brushing
Brush metal finishing, unlike plating, is an effective secondary process for removing surface defects. To smooth out a product’s exterior, this finishing process generates a uniform, parallel grain surface texture. To generate this effect, an abrasive belt or wire brush is frequently used. Furthermore, the belt or brush’s single direction can result in slightly rounded edges perpendicular to the grain.
- Powder Coating
Powder coating creates a decorative finish that is similar to painting but with greater durability. The method entails melting dry plastic powder onto metal to create a textured, matte, or glossy finish. A textured powder-coating process can also be used to cover up existing surface flaws in an simple and effective manner. - Sand Blasting
Sandblasting process is commonly used in projects that require a consistent matte texture. Sand, steel shots, metal pellets, or other abrasives are blasted into a substrate at high speeds in this process (also known as bead blasting). It produces a smooth, clean product texture, which is especially noticeable in soft metals. - Plating
Plating process coats or changes the surface of a substrate with a thin layer of metal, such as nickel or zinc, using a chemical bath. Electroplating coats the substrate with an electric current, whereas electroless plating uses an autocatalytic approach where the substrate catalyzes the reaction. As a finishing technique, plating has a number of advantages, including improving a product’s durability, corrosion resistance, surface friction, and exterior appearance. Plating process, on the other hand, aren’t designed to smooth out surface flaws. - Blackening
Blackening process applies a thin coating of black oxide over a product’s surface to generate a matte black finish with exceptional abrasion resistance. The product is placed into a sequence of tanks containing cleansers, caustics, and coolants during the high-temperature procedure.
3. General Advantages Of Applying Secondary Finishing Treatments
Here are some of the general advantages of applying this secondary finishing treatment to a metal or plastic part, including –
- Increased durability
- Improved decorative appeal
- Enhanced electrical conductivity
- Higher electrical resistance
- Higher chemical resistance
- Higher tarnish resistance
- Potential for vulcanization
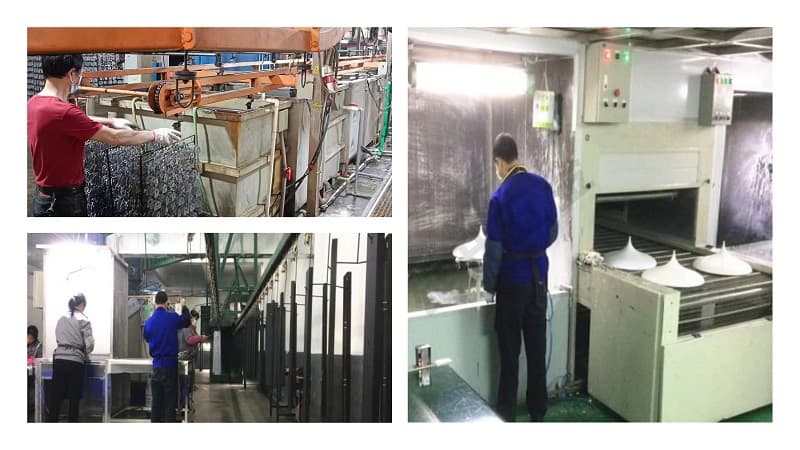