Your Magnesium Die Casting Partner @GEMS-MFG
In conclusion, magnesium die casting is a versatile and efficient process for manufacturing complex metal parts. It offers numerous advantages, including reduced weight, high strength, and cost-effective production capabilities. With a wide range of applications across industries, magnesium die casting continues to be a valuable manufacturing process. Understanding its technical intricacies is crucial for harnessing its full potential in modern manufacturing.
Therefore, in the world of magnesium die casting, your business partner like GEMS-MFG can be the key to unlocking your company’s full potential. We can bring expertise, custom solutions, quality assurance, cost efficiency, and timely delivery to the table. With a collaborative and sustainable approach, we help you succeed in today’s competitive manufacturing landscape, ensuring a long-lasting partnership built on trust and excellence. Choose your business partner for magnesium die casting wisely, and watch your manufacturing endeavors reach new heights of success. To get started, please request a quote through our convenient online form or call us.
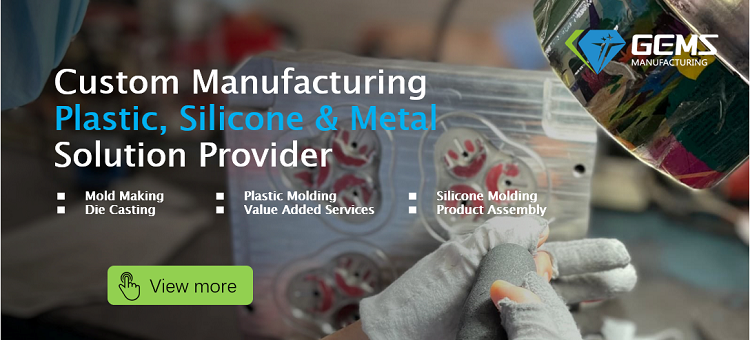