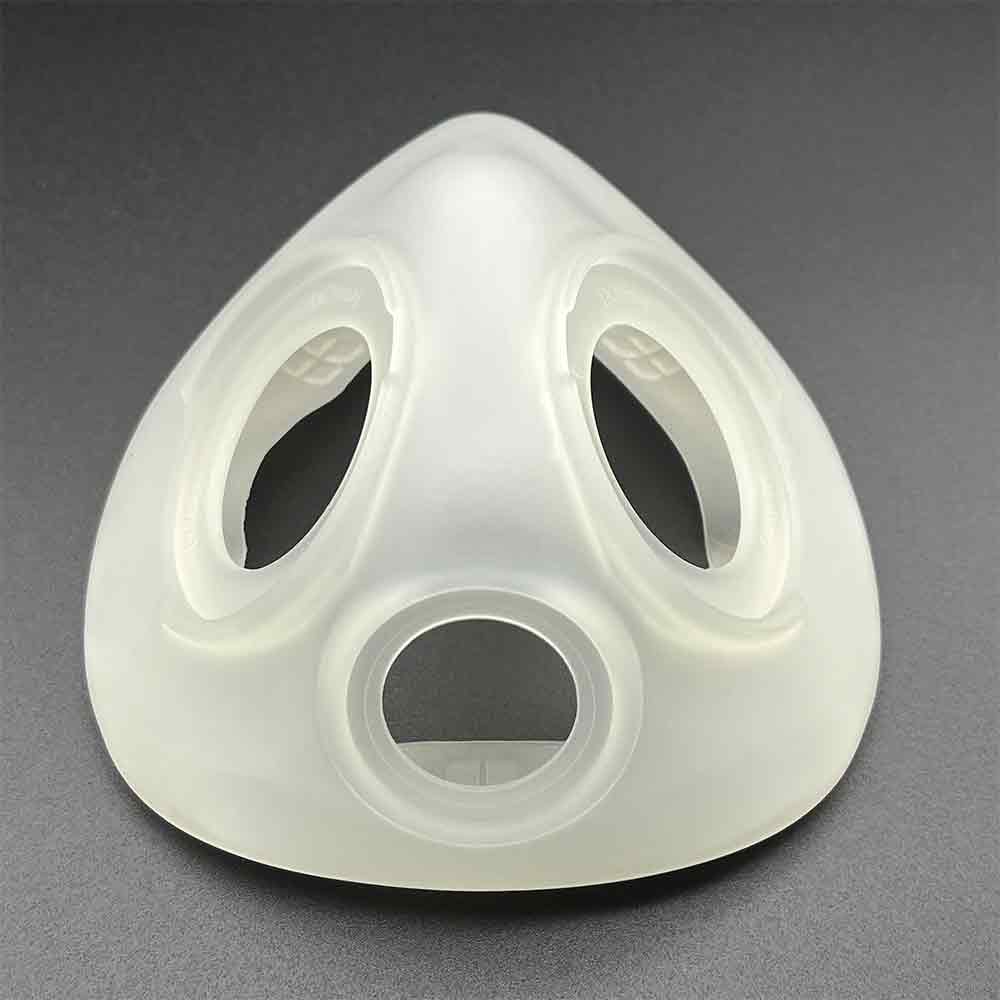
Introduction
- Brief Overview of Injection Molding:
Injection molding is a pivotal manufacturing process renowned for its adaptability in transforming materials into a multitude of shapes. While commonly associated with plastics, injection molding extends its capabilities to a diverse range of materials, including metals and silicones. This highly versatile process revolves around injecting molten material into precisely designed molds, facilitating the creation of intricate and customized components.
The process ensures remarkable precision and repeatability, allowing for the rapid production of complex geometries. This flexibility has positioned injection molding as a fundamental method for crafting parts across various industries.
- Significance in Mass Production of Plastic Parts and Beyond:
Injection molding holds immense significance in the realm of mass production, offering an efficient and cost-effective solution for creating identical components. It has transcended the confines of plastic molding, proving equally adept in handling metals and silicones. This adaptability broadens its application spectrum, making it an indispensable technique for a variety of materials and industries.
Whether shaping plastics, molding metals, or casting silicones, injection molding remains a driving force in modern manufacturing. Its ability to accommodate diverse materials underscores its importance in the creation of components that form the backbone of countless products.