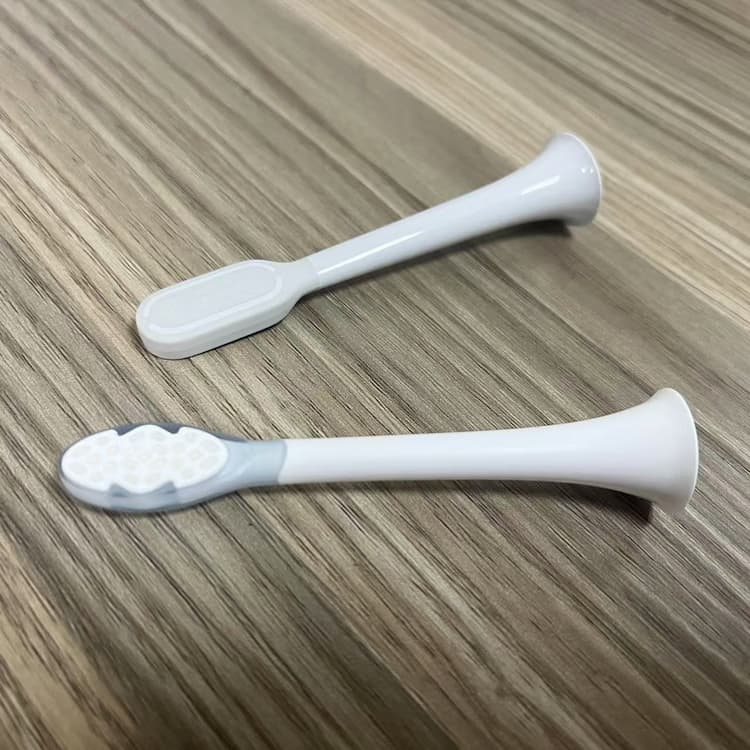
I. Introduction to 2K Injection Mold
2K injection molds, also known as two-shot molds, two-color molds, or 2-component molds, are at the heart of advanced injection molding techniques. This mold allows the creation of multi-material or multi-colored components in a single manufacturing cycle. Unlike standard molds, 2K molds are equipped with mechanisms that enable the injection of two different materials or colors into one mold, either through rotating cores or independent cavities.
This technique is critical for producing parts with enhanced aesthetics, improved mechanical properties, or multiple functionalities. They set the stage for achieving precise tolerances and seamless material bonding. For example, 2K molds are widely used to combine hard plastics with soft elastomers, ensuring durability and ergonomics in products like automotive grips and electronic device casings.
Why Choose 2K Molds?
- Efficiency Gains: Reduces assembly time by consolidating production steps.
- Enhanced Design: Allows for intricate geometries and multi-material designs.
- Cost-Effectiveness: Lowers labor costs and assembly errors by producing a unified part.